A Community Water System in north Texas had a big problem. Their 15,000 gallon pressure tank blew up. The pictures do not do justice as they were taken several months after the fact. The cinder block building containing the pressure tank was completely destroyed. The end of the steel tank that is missing, actually flew into the overhead electric lines and shorted out the electricity for the entire community. A newly installed air compressor on the tank that was not adjusted properly is taking the blame. However, many things can cause a tank to explode.
Thank goodness it happened in the middle of the night, and when no one was around or it could have caused injury or even death.
Power was restored and the debris was trucked away but, the community was still out of water. A 15,000 gallon pressure tank is not a stock item. So it would be several months before a new tank could be procured. In the interim, a 4" Cycle Stop Valve and an 80 gallon diaphragm tank were used to control the 400 GPM fresh water pump. The CSV and 80 gallon tank have a combined retail price of less than $3,000.00. A new 15,000 gallon pressure tank installed is going to cost the community close to $50,000.00.
After several months of working on the CSV with the 80 gallon tank, the community is very pleased with the results. The pressure is more constant than before, and the electric bill is still relatively the same. The CSV and small tank were installed in a small adjacent building, so a big building, which will also be expensive to construct and heat, has not needed to be built.
There is an above ground tank that stores plenty of water to be used as needed. So the supply pump, with CSV, and small pressure tank are required to deliver varied flow rates at a constant pressure. Of course the CSV does a good job of this, as it can supply as little as 5 GPM in the middle of the night, to as much as 400 GPM during times of peak demand, while maintaining a constant pressure.
There really is no need, and the community does not want to replace the 15,000 gallon tank. Not only are they afraid of the potential explosive hazard but, they do not want to spend upwards of $50,000.00 on a water system that is working better than ever before.
The problem is, the State of Texas is decades behind the technology available. I have tried many times since 1994 to explain this technology to State of Texas Engineers, as well as State Representatives. I don't want to say that they can't understand this simple technology but, they certainly do not care to even try. I have been told many times that this system looks really good but, legislation would have to be changed before they could even consider it.
In the meantime, huge pressure tanks are exploding, countless gallons of water are being wasted to leaks in the system, and millions of dollars are being wasted on huge pressure tanks and water towers, that are no longer needed.
I wonder if the Texas State officials have ever read the "Mission Statement" that they send out with every licence and document.
The Mission of the Texas State Government
"Texas State Government must be limited, efficient, and completely accountable. It should foster opportunity and economic prosperity, focus on critical priorities, and support the creation of strong family environments for our children. The stewards of the public trust must be men and women who administer state government in a fair, just, and responsible manner. To honor the public trust, state officials must seek new and innovative ways to meet State Government priorities in a fiscally responsible manner".
Texas State Officials DO NOT seek new and innovative ways but, actually REJECT new and innovative ways without justification. Even though the rules allow for variances to test new and innovative ways, I have been informed in writing that the State of Texas will not issue a variance to try a system with a pressure tank of less than approved size.
What happens now is that when a State Inspector comes by this community water system, it will not pass inspection because of the small pressure tank. Then the city will have to beg for grant money, as they cannot afford the $50,000.00 + price for a new huge pressure tank. The system will work as is for several years, while grant money is being procured. Then tons of money that could have been better used on roads, schools, and other things needed, will be used to return the water system to an outdated control system. I cannot even give the name of this community or they will be tracked down immediately and forced to spend lots of money reverting back to the old way of doing things.
This is just one of many systems that this has happened to in the last 15 years. Texas is not the only state which has this problem. Montana has had plenty of opportunities to test new technology over the years, and still Montana State engineers refuse to come to the 21st century.
It is public money that our public servants are wasting, because of their lack of knowledge. Don't accept their standard answer that it is not in the rules. The rules for the State of Texas were written in the 1950's. We have come a long way since the 50's, shouldn't our government officials be forced to keep up? Or do we just continue to let them keep wasting our money and our fresh water supplies?
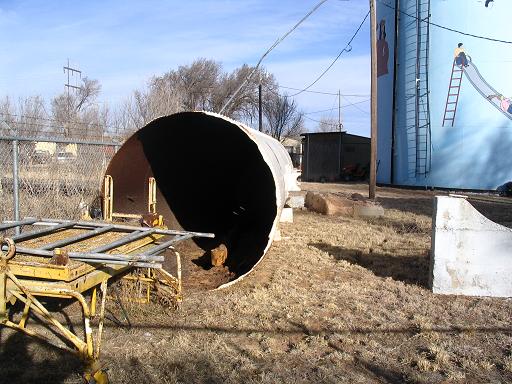