Not to steal a line from one of those cheesy
infomercials on television, but the slogan
for a Cycle Stop Valve could be, “Set it, and
forget it.”
That’s what Low’s Ready Mix Inc., a state-ofthe-
art and newly constructed concrete manufacturing
plant in Caldwell, Idaho, recently found out.
No easy project, Low’s Ready Mix required
instantaneous flow rates of water at a maximum 900
gallons of water per minute when filling concrete
mixers and minimum flows down to 9 gpm to run
the business office when it is not batching concrete.
If that wasn’t difficult enough, the plant required that
this wide range of Low’s be delivered at a constant
pressure.
Hmm. What to do?
Brad Herrick, project manager for Low’s, did
what anyone else would. He asked an expert.
Herrick consulted with Hydro Logic Inc., a hydrogeological
consulting firm in Boise, Idaho.
And the answer?
“We went with Cycle Stop Valves because we had
such a wide range of flow rates. It is difficult to get a
variable-frequency drive that will cover such a wide
range,” says Ed Squires, president of Hydro Logic,
who began using CSVs five years ago.
“The CSV operates throughout the necessary flow
rates. Another reason we specified CSVs is because
the concrete plant has rapidly shutting valves that are
nearly instantaneous. In this new plant, the water
shutoff valves slap shut, a situation that can lead to
water hammer. The CSVs can react more quickly than
a VFD, which can help eliminate water hammer.”
Squires oversaw the installation of an 8-inch
CSV3B for the main water supply well on a 75 hp
pump when the Low’s plant opened in 2006. After a
year of monitoring the plant’s actual water usage
patterns, Squires designed Low’s second (backup)
well with two submersible pumps. In this second
well, flows are regulated by a 6-inch CSV3B. This
valve controls the output for both a 3 hp and 75 hp
pump. Both wells are independently functional, but
the second well with two pumps now serves as the
primary well because of its dual pump capability.
The CSV causes the amp draw of the 3 hp to
vary from 4.6 amps to 2.5 amps, and the 75 hp to
vary from 107 amps to 58 amps. This varies the amp
draw of the system from 2.5 amps to 107 amps,
depending on the amount of flow being used at the
time. Many people do not realize that the power consumption
of a pump when controlled with a valve is
very similar to the power consumption of a VFD
controlled pump. The two-pump setup using the CSV
for control delivers even more energy efficiency and
versatility.
“The CSV really showed its versatility by regulating
a multiple pumping system through a single
valve,” Squires says, “and the manufacturer’s technical
support is beyond compare.”
Another feature of a CSV that is helpful to
Low’s Ready Mix is the part about setting and forgetting
it. The valve’s discharge pressure setting is
adjustable, allowing it to fit the user’s needs. At the
plant, both CSV3B’s have a discharge pressure of
72 psi to 74 psi, with the pressure switch shutoff at
95 psi.
“We find that once the valve is set, it remains
set. That is one of the attributes of these valves,”
Squires says. “They’re very maintenance-free, and if
you do need to adjust them or work on them, all you
need is a crescent wrench. That appeals to a lot of
our clients because most operators like things that
are simple.
“Low’s main focus is making concrete, so they
want a water system that you set and forget. The
CSV, to a large degree, has provided that kind of
system for them.”
No service has been needed for Low’s CSV,
Squires says. He noted the valve’s durability by
recalling another CSV story.
Squires had recommended a CSV for a greenhouse
irrigation well on the outskirts of Boise. The
CSV was installed by one of the client’s employees
and reported it to be “working fine.” Five years later,
Squires and his staff were working on a geothermal
project for the same client and happened to go by the
greenhouse well that had been equipped with the
CSV. However, no CSV was apparent at the well,
which was located in an open field. Nearby, after
looking under a makeshift cover, Squires found the
CSV that had been simply buried in the dirt outside
the wellhead.
“It was still clicking away,” Squires says with a
laugh. “The valve had been working that way since
installation. Now we wouldn’t recommend that,
mind you, but talk about ‘set it and forget it.’”
As for the Low’s project, the only hiccup came
not because of the valve, but rather fist-sized chunks
of concrete that had gotten into the water lines during
installation. Despite the debris, the valve still
worked, but not as smooth as Squires and his staff
thought it should. After checking everything else,
Squires opened up the valve and observed the concrete
chunks had been “beating around” in the valve.
Although there was damage to the epoxy lined
waterways, after the debris was removed, Squires
says “the valve still worked. However, CSV loaned
Low’s another valve to use while they repaired the
epoxy lining in the damaged valve.”
Low’s 3 hp pump will function over flow rates
of 5 to 35 gpm. Once it exceeds that range, the 3 hp
pump kicks off and the 75 hp pump turns on to meet
the increased demand. Low’s can batch 180 cubic
yards an hour on a busy day, dispatching 15 trucks
an hour. Not only that, but the CSV also accommodates
fire-flow requirements of 1100 gpm.
Keeping the Pressure On
Hydrogeological consulting firm designs Cycle Stop Valve controlled pump systems to meet the difficult demands for
a concrete manufacturing plant.
By Mike Price
20/ May 2008 Water Well Journal NGWA.org
An aerial shot of Low’s Ready Mix Inc., a concrete manufacturing plant, in Caldwell, Idaho. Low’s can batch
180 cubic yards an hour.
Mike Price is the Associate Editor
of Water Well Journal. He can be reached
at mprice@ngwa.org
Cycle Stop Valve — 8-inch CSV3B
for backup supply well
Cycle Stop Valve — 6-inch CSV3B
for primary supply well
focus on pumps
“This is just working out great now because
when we need 5 to 600 gpm for a minute or two, the
75 hp clicks on and satisfies that demand, and when
that’s over and it’s slow, and we need to just use 10
to 15 gpm, the 3 hp until we have a big demand
again,” Herrick says. “We’ve got a unique situation
here. I think we’ve got the best of both worlds now.”
Cycle Stop Valves Inc. of Lubbock, Texas,
received its first of five patents in 1999. Cycle Stop
Valves are pump-control valves that essentially make
variable-flow pumps out of any constant-speed
pumps. The CSV attaches to the discharge plumbing
and automatically regulates the pump’s output to
match the amount of water required by the user.
They give large pumps small-flow capabilities without
the need for huge pressure tanks, water towers,
or complicated electronic devices.
Cycle Stop Valves come in a variety of sizes and
models from 1 to 12 inches. They can handle flow
rates of 1 gpm to 5000 gpm, with pressure adjustments
ranging from 4 psi to 500 psi.
“It’s very non-labor-intensive,” Squires says.
“When it comes to VFDs, most water system operators
defer to hired consultants owing to the technical
difficulties of the computerized systems, programming,
and software learning curves. Don’t get me
wrong, I’m not trying to knock VFDs, because we
have a lot of VFD applications and clients who use
them.
“What I am saying is that I don’t subscribe to the
general misconception that VFDs solve all problems
and work in all situations because they do not.
There’s a place for both of these systems and there
are many good applications suitable to using Cycle
Stop Valves where they actually work better than
VFDs, and generally speaking, simple is better.”
If only everything in life were that simple. WWJ
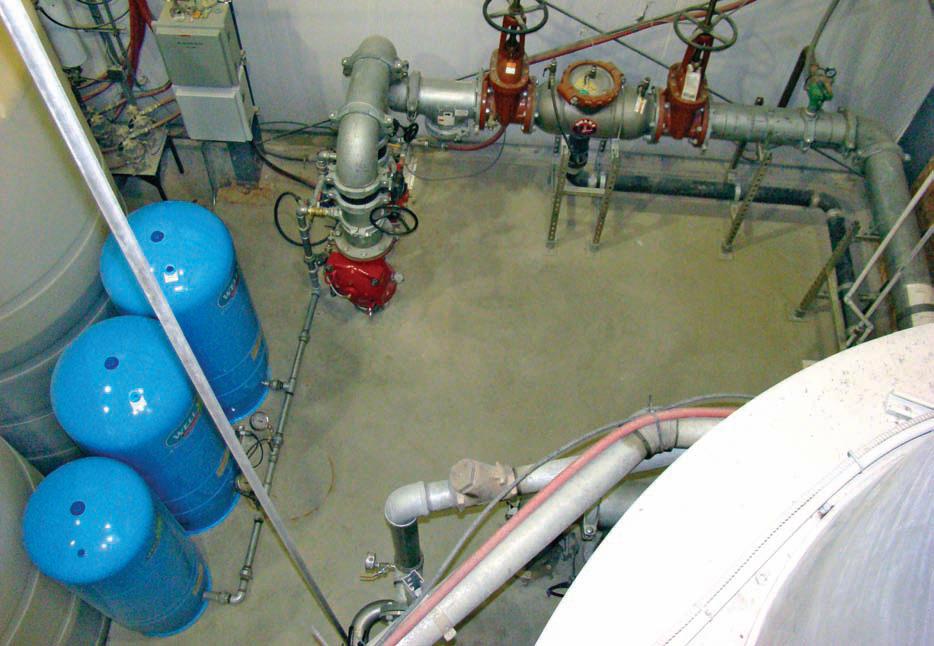